Best Selling Products
5 Popular Printing Techniques in the Modern Printing Industry
Nội dung
- 1. Offset Printing – The top choice for large quantity printing
- 2. Digital Printing – Flexible and time-saving
- 3. Silk Screen Printing – Sophisticated on every material
- 4. UV Printing – Sharp and innovative with special effects
- 5. Flexo Printing – The optimal solution for packaging and labels
- 6. Conclusion
Explore 5 popular printing techniques in the modern printing industry: from offset printing, digital printing to silkscreen printing. The article provides detailed, easy-to-understand knowledge for designers and marketers.
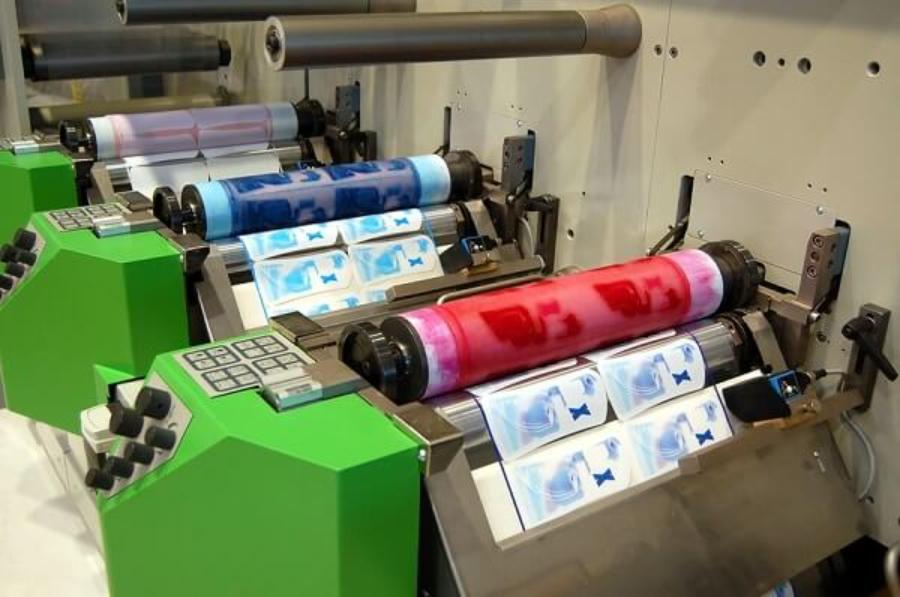
Modern printing is not only the field of producing images on materials but also the art of conveying messages in a subtle way. With the strong development of technology, printing techniques are increasingly diverse, meeting the creative needs of designers and businesses. The following article sadesign will introduce in detail the 5 most popular printing techniques, helping you have a comprehensive view to choose the appropriate method for each purpose of use.
1. Offset Printing – The top choice for large quantity printing
Offset printing is considered the most popular traditional printing method in the printing industry, especially when printing in large quantities. This technology works based on the principle of indirect printing: the ink is not printed directly onto the paper but through a roller system including a zinc plate, a rubber roller (blanket) and a pressure roller.
The offset printing process includes the following basic steps:
Plate making: First, the image or text to be printed is processed on a computer and exported to film. From this film, people will create prints (usually made of metal, called zinc plates) for each different ink color (usually the 4 basic colors CMYK: Cyan, Magenta, Yellow, Black). The printed elements (containing the image) on the zinc plate absorb ink, while the non-printed elements absorb water.
Mounting the printing plate onto the printing cylinder: The zinc plates after being manufactured will be mounted onto the corresponding printing cylinders on the offset printing machine.
Ink transfer and wetting: When the machine is running, the printing rollers rotate. First, the wetting roller wets the surface of the plate. The water only adheres to the non-printing elements. Then, the ink roller rolls over, and the oil-based ink only adheres to the dry printing elements.
Transferring the image onto a rubber blanket: The zinc plate carrying the ink image will come into contact with the rubber blanket. The ink image will be "offset" (indirectly transferred) onto the surface of the soft rubber blanket.
Pressing onto the surface of the printing material: Finally, the rubber roller carrying the ink image will press onto the surface of the printing material (paper, cardboard,...) under the pressure of the press roller. The ink from the rubber roller will adhere to the material, creating the final print.
Outstanding advantages:
Stable image quality: Thanks to indirect printing technique, printed images are always clear, with even colors and no smudging.
Economic efficiency: When printing in large quantities, the cost per unit of product is greatly reduced.
Ability to print on many materials: From couche paper, fine art paper to high-quality paper can all be applied.
Popular applications:
Offset printing is often used in printing books, magazines, brochures, catalogs, name cards, paper packaging... This is the ideal technique for publications that require high accuracy in color and design layout.
2. Digital Printing – Flexible and time-saving
Digital printing is a modern printing technology that allows data to be transferred directly from the computer to the printer without having to create a print plate like offset. Thanks to this feature, this method is very suitable for small orders or quick printing requirements.
Working principle:
There are two main digital printing technologies:
Inkjet Printing: The inkjet print head contains thousands of tiny nozzles that are capable of spraying extremely small ink droplets onto the surface of the printed material according to images controlled by the computer. These ink droplets will combine on the material to form the final image. Inkjet printing technology is widely used in office printing (personal printers), photo printing, large-format advertising printing (banners, posters), and printing on special materials (fabric, decals...).
Laser Printing: In laser printing, a laser beam draws an electrostatic image onto a magnetic drum. Dry, oppositely charged toner particles adhere to the charged areas on the drum. The toner is then transferred to the paper and melted to adhere to the paper. Laser printing is commonly used for printing text, documents, and moderate-volume black-and-white or color publications.
Outstanding advantages:
Time saving: No plate preparation required, allowing immediate printing.
Reasonable cost for small orders: No need to invest in printing, so the price is suitable for personal needs or design testing.
Easy to customize content: Suitable for printing variable data such as personalized invitations, employee cards, vouchers with individual names.
Popular applications:
Digital printing is widely used in office printing, poster printing, event flyers, restaurant menus, labels, invitations and many other types of personalized publications.
3. Silk Screen Printing – Sophisticated on every material
Screen printing is a popular hand-printing method for artistic and unique products. This technique uses a screen coated with a photosensitive adhesive, then exposed to light to create a screen, allowing ink to pass through the unobstructed areas.
Working principle:
The screen printing process includes the following main steps:
Creating the printing plate: First, the design to be printed is transferred onto film. The plate is made by stretching a silk or synthetic mesh with small, even holes over a frame. A layer of light-sensitive chemicals is then applied to the mesh. The printing film is placed on top of the chemicals and exposed to light. The light hardens the chemical parts not covered by the film. Finally, the plate is washed with water to remove the unhardened chemicals, creating open mesh holes corresponding to the image to be printed. The unprinted parts are sealed with a special glue.
Prepare printing material: The material to be printed (t-shirt, cloth bag, plastic, wood...) is placed flat under the printing plate.
Squeegee: Ink is poured onto one end of the mold. The printer will use a squeegee blade, with a certain force and angle, to squeegee the ink evenly across the surface of the mold. The ink will seep through the open mesh holes and adhere to the surface of the material below.
Drying: After printing, the product will be dried to ensure the ink adheres firmly and is durable. For some special inks, additional heat or chemical processing steps may be required.
Multi-color printing: For multi-color designs, each color will need its own printing plate and be printed one after the other, requiring precise alignment between the color layers.
Outstanding advantages:
High color fastness: The ink has high adhesion and is difficult to fade, especially when printed on fabric or waterproof surfaces.
Create special effects: Can be applied with glitter ink, reflective ink, or embossed to create tactile effects.
Suitable for hand printing and handmade products: Especially suitable for highly handmade products such as hand-printed t-shirts, canvas bags, art posters.
Popular applications:
Screen printing is often used in fashion, souvenirs, decorative posters, handmade products and highly personalized designs.
4. UV Printing – Sharp and innovative with special effects
UV printing is a technique that uses special inks that dry immediately under the influence of UV rays. Thanks to this mechanism, the printed image is not only sharp but also has a customized gloss or matte finish, increasing the visual effect of the product.
Working principle:
Unlike traditional printing techniques where the ink dries by penetrating the material or evaporating the solvent, UV inks are made up of monomers and oligomers that are sensitive to UV rays. When the ink is printed on the surface of the material, it is immediately irradiated with a UV lamp of the appropriate intensity. Under the influence of UV rays, the ink molecules will react chemically, forming a solid polymer film that adheres tightly to the printed material. This process takes place almost instantly, preventing the ink from smudging or smearing and creating a dry printing surface immediately after printing.
Outstanding advantages:
Vivid colors: UV inks are often very dense and have high color coverage, creating vibrant, realistic images and colors. In particular, because the ink dries quickly, the phenomenon of color bleeding or inaccurate color overlap is significantly reduced compared to some other printing techniques.
Diverse surface effects: One of the special features of UV printing is the ability to create many unique surface effects. By adjusting the amount of ink and UV intensity, people can create glossy, matte, or even locally embossed surfaces, coated with UV varnish to highlight and enhance the aesthetics of the design.
Can print on many types of materials: UV printing technology has good adhesion on many different types of materials, including difficult-to-print surfaces such as plastic (PVC, PET...), mica, glass, wood, metal, leather, fabric, and many different types of paper. This opens up many potential applications for this printing technique.
High durability: The UV ink layer after drying has very high durability, is scratch-resistant, waterproof and resistant to environmental impacts, helping to protect printed images for a long time.
More environmentally friendly: Compared to some traditional printing inks that contain volatile solvents, UV inks often have lower VOCs (volatile organic compounds) content, thus causing less environmental pollution.
Disadvantages:
High ink costs: UV inks are often more expensive than conventional inks.
High equipment investment cost: UV printers and UV lamp systems have quite high initial investment costs.
Requires specialized operating techniques: The operation and maintenance of UV printers requires highly specialized technicians to ensure print quality and safety during the use of UV rays.
Popular applications:
UV printing is suitable for high-end products such as luxury name cards, advertising signs, gift boxes, interior design, or even decorative art paintings.
Thus, UV printing is an advanced printing technique, providing the perfect combination of sharp image quality and unique surface effects, meeting the increasing demand for aesthetics and differentiation in printing.
5. Flexo Printing – The optimal solution for packaging and labels
Flexographic printing is a relief printing technique, using a printing plate made of soft polymer, operating similarly to traditional typo printing. This method was specially developed for printing on roll materials such as nylon, plastic film, kraft paper, cardboard.
Detailed operating principle:
The flexographic printing process is a series of coordinated steps to transfer the image from the printing plate to the material surface:
Flexographic Printing Plate Making: Flexographic printing plates are created by etching or photochemically forming soft rubber or polymer plates. The printed elements (images, text) are raised on the surface of the plate, while the non-printed elements are located on the lower surface. The plates are usually mounted on cylinders, sized to accommodate the repeat length of the printed design.
Closed ink supply system: The ink (usually a water-based, oil-based or UV liquid ink) is contained in a closed ink supply system, consisting of an ink tank and one or two doctor blade systems. The anilox roll, a metal roller with a surface laser-etched with thousands of cells of uniform size and shape, rotates and is partially immersed in the ink tank. Excess ink on the surface of the anilox roll is scraped off by the doctor blade, ensuring that a precise amount of ink is contained in the ink cells.
Transfer of ink to the printing plate: As the anilox roll continues to rotate, the surface containing the ink in the cells will contact the raised surface of the flexo printing plate. The gentle pressure between the anilox roll and the printing plate will transfer a thin and uniform layer of ink to the raised printing elements of the plate. The amount of ink transferred is controlled by the size and number of cells on the anilox roll.
Printing process: Roll-shaped printed material (e.g. plastic film for making nylon bags) will be guided between the printing cylinder carrying the ink plate and the impression cylinder. The impression cylinder creates a stable pressure, forcing the material into contact with the printing cylinder carrying the ink. Thanks to this pressure, the ink from the embossed printing elements on the cylinder will transfer to the surface of the material, reproducing the image or text to be printed.
Drying and Cooling: Immediately after printing, the material passes through a drying system. Depending on the type of ink used (water-based, oil-based or UV), the drying system can use hot air, infrared (IR) rays or UV lamps to dry the ink quickly and ensure good adhesion to the material surface. After drying, the material can be cooled to prepare it for further processing.
Integrated post-press: One of the great advantages of modern flexo presses is the ability to integrate multiple post-press processes directly on the same line. Modules such as lamination, die-cutting for special shapes of labels or packaging, creasing, perforation and slitting can be installed in series with the printing unit. This increases production efficiency and reduces the time and cost of transportation between processes.
Outstanding advantages:
High printing speed: Designed for mass production with continuous roll system.
Optimized for flexible packaging: Well suited for printing on soft, flexible materials or non-flat surfaces.
Synchronous laminating and die cutting capabilities: Suitable for modern industrial production lines.
Popular applications:
Flexo is often used in the packaging industry, bottle labels, plastic bags, product labels, food boxes, toilet paper, candy bags... In particular, this is an indispensable technique in the FMCG (fast moving consumer goods) sector.
In particular, flexo printing is an indispensable technique in the FMCG (fast moving consumer goods) sector. FMCG products often have a short life cycle, large output, and require eye-catching packaging and low production costs. Flexo printing fully meets these requirements, playing a key role in effectively bringing products to consumers.
6. Conclusion
Each printing technique has its own advantages and is suitable for different purposes. From the precision of offset printing, the speed of digital printing, to the creativity of UV printing or the handmade feel of screen printing – all contribute to shaping the appearance of the final product. Understanding the characteristics and application capabilities of each technique will help you optimize costs, ensure quality and create a professional impression in the eyes of customers.